中村 茂弘
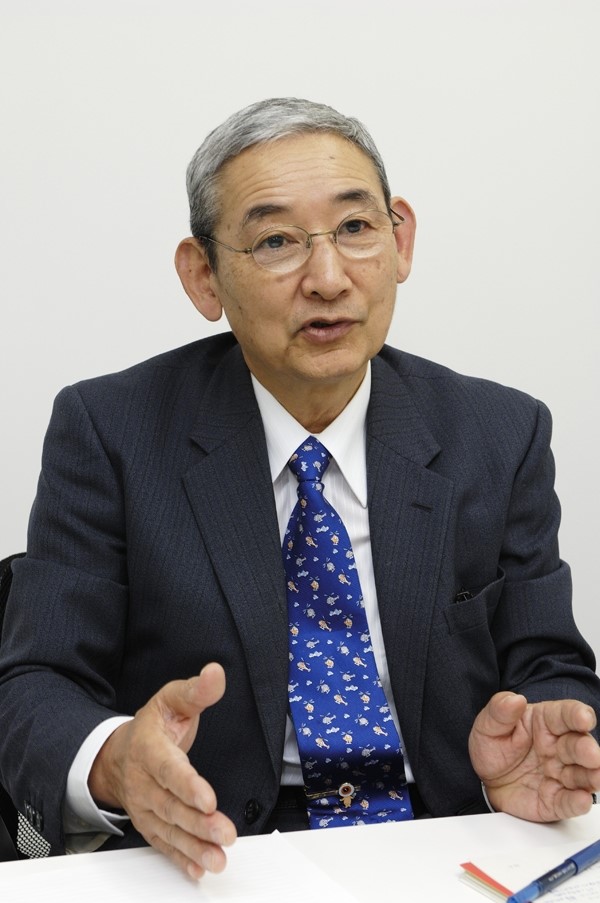
QCD革新研究所 (屋号) 所長
一般社団法人 日本能率協会 講師歴任
ストアカ(Zoomセミナー担当講師)
講師カテゴリー
- 経営・ビジネス
- マーケティング・イノベーション・ブランディング
- ものづくり・製造業
- ビジネス研修
- リーダーシップ・マネジメント
- コーチング
- 問題解決
- DX・AI・IoT・IT・5G・ビッグデータ
- DX・AI・IoT・IT・5G・ビッグデータ
- スポーツ
- その他スポーツ
出身地・ゆかりの地
東京都
この講師について問い合わせる
お急ぎの方はお電話ください
- 東日本
03-3249-0666 03-3249-0666 - 西日本
06-6312-0691 06-6312-0691
プロフィール
昭和18年生まれ
昭和45年早稲田大学理工学研究所 金属工学科大学院卒
昭和45年~平成2年 日立金属株式会社にて、新製品開発担当、IE/QC/VE/JIT/CIM
など改善・管理技法を駆使した各種プロジェクトを指導・担当。
内、米国AAP St.Marys社に3年赴任。
平成2年~
一般社団法人日本能率協会専任講師開始、
TP賞審査委員を担当開始。(有)QCD革新研究所(現在、屋号化) 代表取締役
ISO9001、ISO14001審査員補、CPC(個人情報保護コンサル資格)、経産省・技術継承支援者認定者
剣道7段、目黒清釣会・会長歴任
講演テーマ
【技術伝承の実践ノウハウを学ぶ】
1,少子高齢化と製造業の今後への影響
2,匠技術の解析と伝承のコツ(技術・技能伝承テーマの仕分けとMAP解析)
3,適正評価と人材確保
4,85%以上を決める習得術
5,伝承に効果的なコーチング
6,研究会で実践して得た伝承法の要点と適用事例~まとめ
【不良・クレームゼロ対策について】
1,歴史の整理で判る不良ゼロ対策の王道
2,事例に学ぶ「品質事故と社会的影響」:コンプライアンス問題に見る品質コストとその影響
3,演習で学ぶ「わいわいガヤガヤ不良対策方式」の見直し
4,「3現主義」の実務展開法の体得
5,不良発生予防に必要なハザードMAP・「見える化」対策
6,ヒューマン・エラー・ゼロ撲滅手順の実際
7,原理図化法による原因追及~完全除去対策の実務
8,不良予備軍の発掘~発生防止徹底の実務
9,品質改善からダントツ品質へ向けて
【SCM実現のための物流対策(構築)セミナー】
1, JIT・SCM納入の必要性
2, 工場内物流の問題把握~棚卸し(含むコスト対策)
3, 物流改善の手順
4, 科学的な在庫理論と発注方式の評価法(OR)
5, 梱包・発送業務における仕事量変動対策
6, 発注先、工場における物流対応
7, 情報ネットワーク対策とIT活用
8, 物流VEと全員参画体制
【経営財務分析と原低対策】
1,収益確保と現場改善の必要性
2,図化して判る経営財務のすべて
3,損益計算書の図化と原低対策!
4,貸借対象表の図化と財務改善!
5,CF解析で不正行為は解明可能!
6,原価低減策、ハウツウを一覧化
【新製品開発設計段階からのターゲットコスト対策】
1,設計・開発段階に85%の原低要因
2,ターゲットコスト対策と実践例
3,ターゲットタイム視点で原価革新
4,DCで掘り起こすカラクリ・潜在原低
5,SDGs時代に高まる攻めの原低!
【サプライヤーの品質評価~早期品質向上指導法】
1,サプライヤー評価
2,サプライヤー自身が自主的に体質強化を図る指導法
3,品質向上活動に向けた「品質コスト」運用法
4,協力会社が身につけるべきスピード不良ゼロ解析法
5,グローバル企業におけるスピード・自律的品質向上対策指導法
6,不良発生予防のためのISO活用と監査の実務
【社外クレームゼロ~品質管理・保証の徹底対策】
1,各種コンプライアンス事件解析で判る品質管理・保証問題
2,成果を挙げてきた事例に見る標準化の容易化・徹底活用法(含むポカヨケ対策)
3,実のある強力な実務品質監査法(見直し~強化ポイント:品質管理・保証責任体制など)
4,オトリ作戦によるQTAT品質改善(ハインリッヒの原則活用:ヒヤット段階で不良撲滅)
5,IoT時代の見える化+品質保証(トレーサビリティもIT化)
【グローバル工場の工場の生産力・指導力向上対策】
1,日本産業のグローバル展開とリスク対策
2,現地との融合~強い組織・生産体制構築法
3,スピード技術移管~不良を出さない生産体制
4,現地化に欠かせない「見える化」経営課題の早期実現法
5,未来を託するトップマネージャー~S/Vの効果的育成法
【経営直結型5S改善・実践体得法】
1,整理・整頓~清掃の繰を返す5Sはムダ!
2,5S改善の前に必要な経営分析~対象テーマ発掘を!
3,現場診断~ムダ排除手法の体得
4,体験して判る5S改善効果と関係者の巻き込み(5S改善コスト評価)
5,目に見にくい問題の対策
【スピードIE手法効果の見える化】
1,改善の必要性明示と、原価低減成果の「見える化」対策
2, IE手法の歴史と、高い問題意識を持つ改善リーダーづくり
3,方法改善の技術による~生産性向上のダントツ化
4,ビデオ活用時間分析による「ムダの見える化」(体験学習)
5,ハイ・スピード改善対策~見える化+常時利用使う標準化
【食品産業の『異物混入』根絶対策】
1,食品異物報道の影響~対策探求
2,物的・人的要因、撲滅対策の実務(含む、金属混入ゼロ対策体制づくり)
3,昆虫・小動物混入ゼロ対策の実務
4,髪の毛混入ゼロ対策の実務
5,人手不足時代・IoT時代の総合的異物混入ゼロ・アプローチ
【製造業の自然災害BCP対策(含む新型コロナ対策)】
1,自然災害事例解析とリスク整理
2,BCP 対策に必要なリスク感知と見える化対策
3,ハザード MAP による災害対策の予防と減災の実務
4,初動に役立てる防災訓練の実務
5,サプライチェーンを巻き込むBCP 対策の展開
【IoT時代のJIT・SCM対策】
1,トヨタ開発によるJIT開発の歴史
2,TPS・JITの真似で「生病法で大けが」対策
3,TPS・JITの全技術体系の整理と一覧化
4,JIT・SCMによる徹底ムダ排除
5,JIT・SCM対策に有効な各種改善技術
【生産管理の基礎】
1,生産管理の目的と機能
2,最短・最早モノづくり対策
3,CIM・動態管理とムダ排除
4,生産変動対応~遅延防止
5,SDGs・攻めの生産管理
【工場レイアウト設計法(含むセル生産方式)】
1, キャッシュフロー最適のための生産・販売レイアウト
2, 演習で体得する工場レイアウト設計法
3, 全体最適から部分最適セルへのアプローチ
(含む、ユニットレイアウト改善・セルの最適化)
4,多種少量切り替え生産対策ライン構築手法
5,JIT・SCM効率化に必要な「情報レイアウト最適化」対策
【製造現場の“ケガ・ゼロ:作業安全”対策の実務】
1,「他山の石(他社事例解析力)」によるリスク感知力研磨
2,ケガ発生メカニズム解析の進め方
3,集中力低下から鑑みるエラー対策(含むポカヨケ対策と管理)
4,個人が身につける技の教育~KYT訓練と対策(含む見える化対策)の実務
5,ケガ・ゼロのためのハザードMAP対策
実績
■主な業績
≪企業在勤時代≫
新製品開発パテントMAP手法開発。日立グループIE研修講師、
(昭和45年~平成2年3月) 全社CIM構築、各工場レイアウト新設・改善プロジェクトリーダー、
並びに、指導専門部署歴任、VEC推進部主任技師、他
≪日本能率協会にて≫
(平成2年~現在) 米国・英国・ドイツ、フランス、デンマーク、韓国・シンガポール、ソ連など、海外企業直接指導(10年余り)。国内大手企業の収益増強対策、新製品開発、営業強化指導、
不良・クレームゼロ対策指導(研究会幹事)、リサイクル対策研究会幹事、チームマネジメント研究会幹事、など
講演の特徴
事前にニーズを十分お聞きして講演や研修会の担当をさせていただきます(なお、ご相談・打合せ時は無料)。
Zoomセミナーの場合、1社で数か所のご開催が可能です。
著書
「New-Standardization」
「Go-Go Tools(英語版)」
「標準化技術」
「新・工場レイアウト設計法」、
「海外現地工場運営の実務」
「新製品開発・生産立ち上げスピード化技術」
「攻めの特許とパテントMAP]
「リサイクル設計の技術」
「職・組・班長、自習型教育ツール」
「生産技術部長業務完全マニュアル」
「経営・財務入門」
「不良・クレームゼロ対策テキストブック」
「技能・技術伝承法」
その他、約150冊(含む、Kindle書 英語版14冊、日本語版:現在50冊アップ中です。)
動画
1,qcd.jp 無料文献の利用法ご案内(映像にて解説):https://www.youtube.com/watch?v=gzhniBPipyw&feature=youtu.be
2,On-Line 研修の解説(映像にて解説):http://www.youtube.com/watch?v=qZGddfeGMMw&feature=youtu.be
この講師について問い合わせる
お急ぎの方はお電話ください
- 東日本
03-3249-0666 03-3249-0666 - 西日本
06-6312-0691 06-6312-0691
同じカテゴリーの講師一覧
- 安斎 勇樹株式会社MIMIGURI代表取締役Co-CEO / 東京大学大学院 情報学環 特任助教▶【問いのデザイン:問題の本質を見抜き、本当に解くべき問いを立てる】講師候補に入れる
- 中山 智夫株式会社ITCアエロリーシング 創業者・取締役会長 一般社団法人日本エアレスキュー促進協議会 代表理事 日本チュニジア友好協会 会長▶【ビジネスで如何に成功するか】講師候補に入れる
- 堀田 みきほ訪日インバウンド対応研究家 訪日インバウンド対応総合研究所▶【外国人観光客にトラブルを起こさせない店づくり】講師候補に入れる
- 高橋 浩士スモールビジネスコンサルタント▶【ネット時代の発信力養成セミナー】講師候補に入れる
- 木曽 崇株式会社国際カジノ研究所 所長 株式会社エンタテインメントビジネス総合研究所 客員研究員 諏訪東京理科大学 地域連携研究開発機構 客員研究員▶【講演可能な内容】講師候補に入れる
- 小松崎 雅晴講師候補に入れる
いま注目の講演会講師一覧
- 原 邦雄一般財団法人ほめ育財団 代表理事 株式会社スパイラルアップ 代表取締役/ほめ育コンサルタント▶【ハラスメント防止、中小企業の最大リスクの一つ、労使関係が一気に改善する「ほめ育」420社以上に導入 『部下とのコミュニケーションが一気に改善 “ほめ育”コミュニケーションセミナー』】講師候補に入れる
- 廣田 さえ子 SAEKO HIROTA株式会社デルタマーケティング エグゼクティブプランナー (リクルートトップパートナー代理店所属)▶【リクルート営業9期連続NO.1営業が語る 商談の秘訣】講師候補に入れる
- 伊藤 和人日本経営開発協会 JMDA教育研修センター室長 人材育成コンサルタント▶【職場の多様性を尊重するコミュニケーション】講師候補に入れる
- WマコトCLASSIX株式会社 代表取締役 放送作家(元・吉本芸人) お笑い研修プログラム講師▶【バラエティ現場から学ぶ!『笑撃ビジネスコミュニケーション術』】講師候補に入れる
- 仲内 真弓一般社団法人医療接遇ホスピタリティ協会 代表理事 ▶【WEB セミナー 「今日から実践!アフターコロナ時代の医療接遇」】講師候補に入れる
- 中路 和宏組織改革研究所代表 万松青果株式会社代表取締役会長 中小企業診断士 一級販売士▶【中小企業「わかもの」採用戦略ーブルーカラー編「主人を面接に行かせてもよろしいですか?」】講師候補に入れる
月間講師依頼ランキング
先月の講演依頼のお問合せが多い講師をランキング形式でご紹介
- 1位新井 紀子国立情報学研究所社会共有知研究センター センター長・教授 総合研究大学院大学複合科学研究科情報学専攻教授 国立情報学研究所情報社会相関研究系教授 一般社団法人 教育のための科学研究所 代表理事・所長
▶【わが国の経済成長に向けてAIが果たす役割】講師候補に入れる - 2位
- 3位
講演会の講師派遣レポート
- 2025年03月11日 日本製鉄 橋本会長のご講演―超大企業トップの“腹の据わった不退転の覚悟”を受け取りました!(今春 全国経営者大会講演への感想として①-2【後編】)
- 2025年03月11日 日本製鉄 橋本会長のご講演―超大企業トップの“腹の据わった不退転の覚悟”を受け取りました!(今春 全国経営者大会講演への感想として①-1【前編】)
- 2025年02月19日 <講師派遣レポート> 村瀬健氏 講演会『好かれて、信用されて 買っていただく コミュニケーション術』
- 2025年01月28日 <講師派遣レポート>山口泰信氏講演会『大災害から人命を守り事業を継続させるために~被災経験から語る企業必須の「防災BCP」~』
- 2024年11月29日 <講師派遣レポート>中野信子氏講演会『AIと人間社会の協創社会に向けて』